Executive Summary
As the pharmaceutical industry shifts towards advanced therapeutic solutions utilizing monoclonal antibodies and cell and gene therapies, there is a growing shift towards personalized, smaller batch sizes in contrast to larger batch sizes associated with traditional medicinal products.
Regardless of the size of the batch, the necessity for sampling and quality control testing remains to support regulatory requirements and ensure patient safety.
Given that advanced drug products are typically produced in smaller quantities, conventional analytical testing consumes a disproportionate percentage of the finished product, and the process for sample testing is time-consuming and resource-intensive. These factors are known to severely impact both the cost and time efficiency given the limited availability of small-scale batches.
As a result, there is a need for technical solutions that can complete compendial testing through non-destructive analytical methods, reduce the amount of wasted drug product, and decrease the lead time to deliver advanced therapies to patients.
With this in mind, we were approached by Roche to develop a technical solution that would combine the benefits of our VRU inspection system with Roche’s integrated process analytical technology (PAT) to perform analytical testing of the finished product within closed containers.
How to improve lead time optimizing QC
Options to gain lead time by using Real-time release testing elements
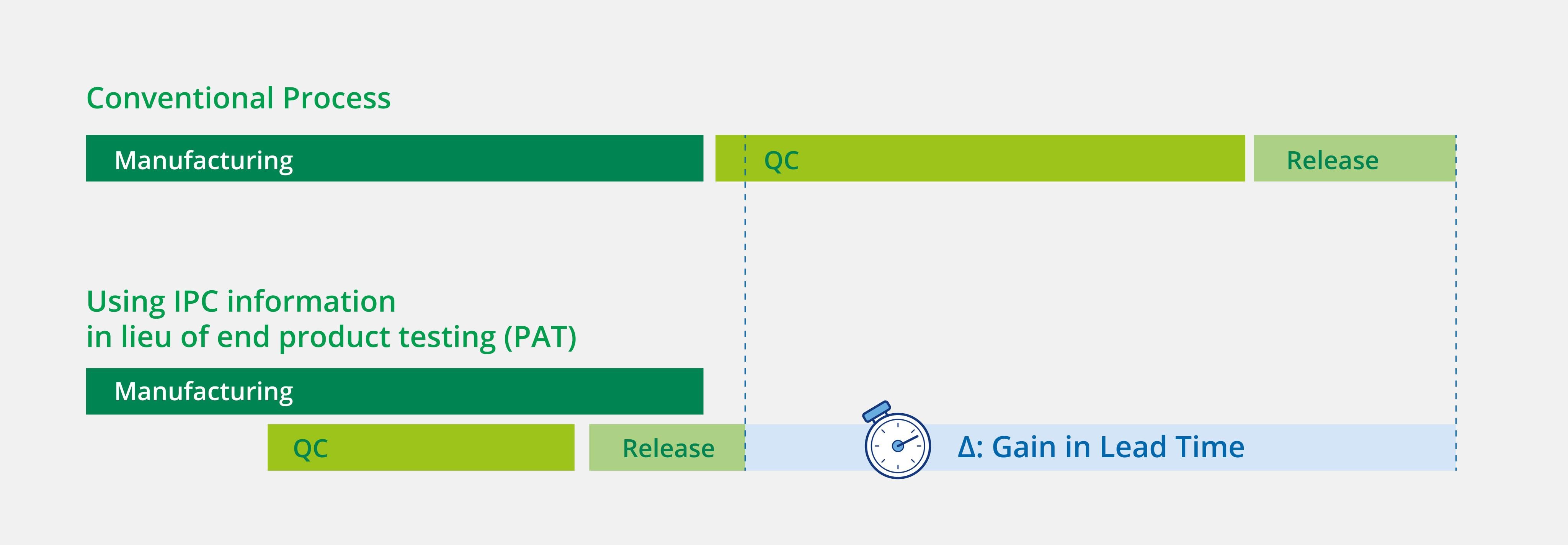
QC: Quality Control - IPC: In-process Control - PAT: Process Analytical Technology
Lead times for typical QC and testing processes
Test Approach
The objective of this study was to develop a solution that would integrate real-time release testing to monitor and measure CQAs (critical quality attributes) through non-destructive analytical tests.
To start, we needed to ensure that non-destructive testing could be performed to monitor and measure physico-chemical attributes of individual batches in-situ, such as:
Appearance: Validate the drug product maintains its expected visual characteristics
Color and Clarity: Monitor and detect any deviations that could indicate quality issues
pH and Osmolality: Measure the parameters to ensure the drug's stability and efficacy
Identity: Verify the identity of the product
Container Closure Integrity: Ensure the packaging maintains a sterile barrier to protect the drug product
Additionally, we needed to ensure that GMP-validated testing could be implemented on existing equipment to ensure GMP-compliant data sets with audit trails and approvals using MVA (multivariate analysis) methods, focusing on the following:
Controlled Environments: The use of controlled settings to maintain the integrity of the drug product during testing.
Calibration Targets: Ensure regular calibration of instruments to ensure accurate and reliable measurements.
Single Container Track and Trace: Implement advanced tracking systems to monitor each container individually, ensuring traceability and accountability throughout the manufacturing process.
Our approach is to combine these testing elements within a single platform.
The Technological Solution
To address this challenge, we integrated our Vision Robot Unit (VRU) technology with Roche’s process analytical technology (PAT). This combination enabled us to perform simultaneous non-destructive testing directly on the inspected containers and data analysis that fully complies with GMP standards.
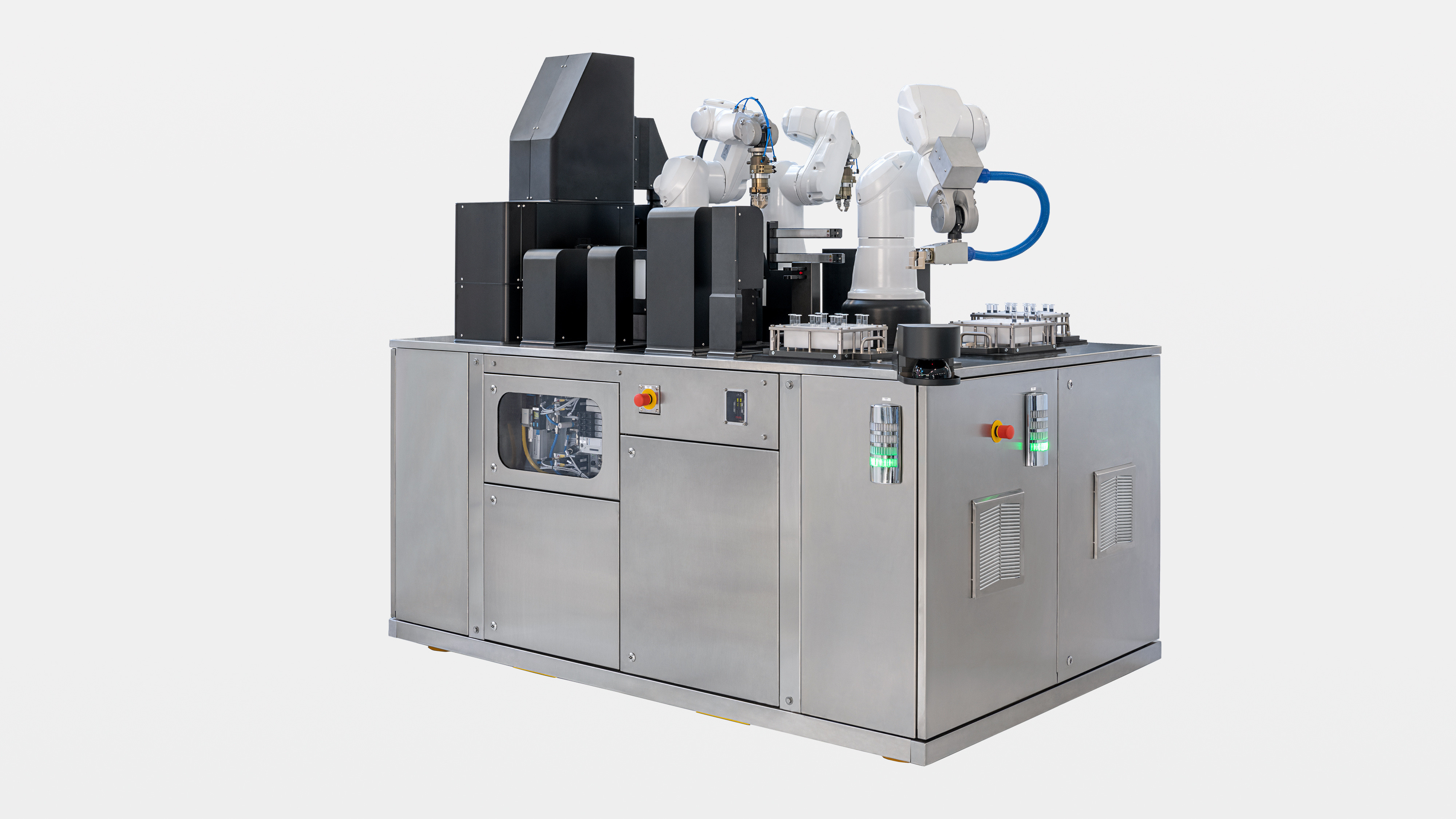
The VRU acts as a robotic human-like inspection unit that combines flexibility with automation efficiency via AI-based machine learning capabilities.
With its high precision inspection, the VRU conducts detailed visual inspections to identify any defects or inconsistencies in the product - keeping detection rates high, but false rejection rate (FRR) low.
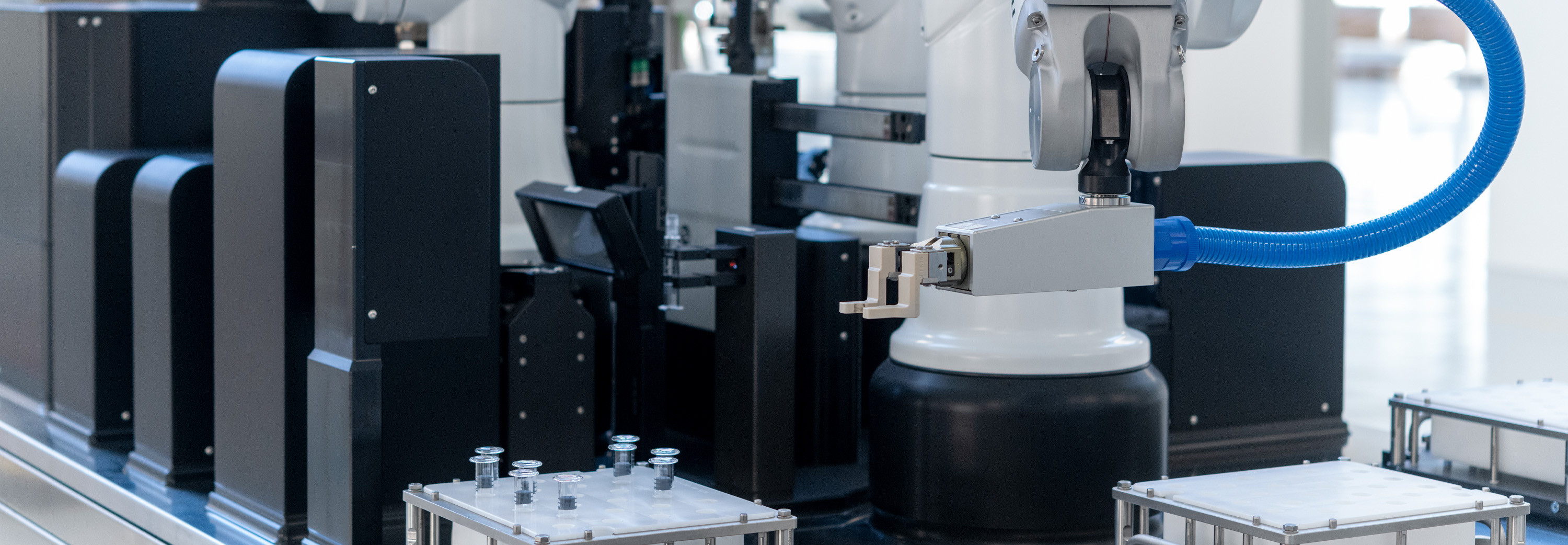
Use of robotic arms
Modularity
Small Batches
Inspection strategy
Human-like inspection
Artificial Intelligence (Deep Learning)
Following the standard inspection by the VRU, the product transitions into the PAT module and compendial testing platform (CTP) to perform the analytical testing concurrently with the visual inspection on the same platform.
Due to its adaptability, the unit can also be easily adjusted to inspect various container types and sizes, accommodating the diverse needs of small batch production where batch sizes and container specifications can vary significantly.
In one example of success, we implemented Raman spectroscopy technology as an example of non-destructive chemical identification testing to distinguish between two similar monoclonal antibodies.
The vision illustrated by a real example
Project example: The Raman finished product identity testing
"Translating Technical Innovation into Operational Context to Bring Our Products Faster to the Patient"
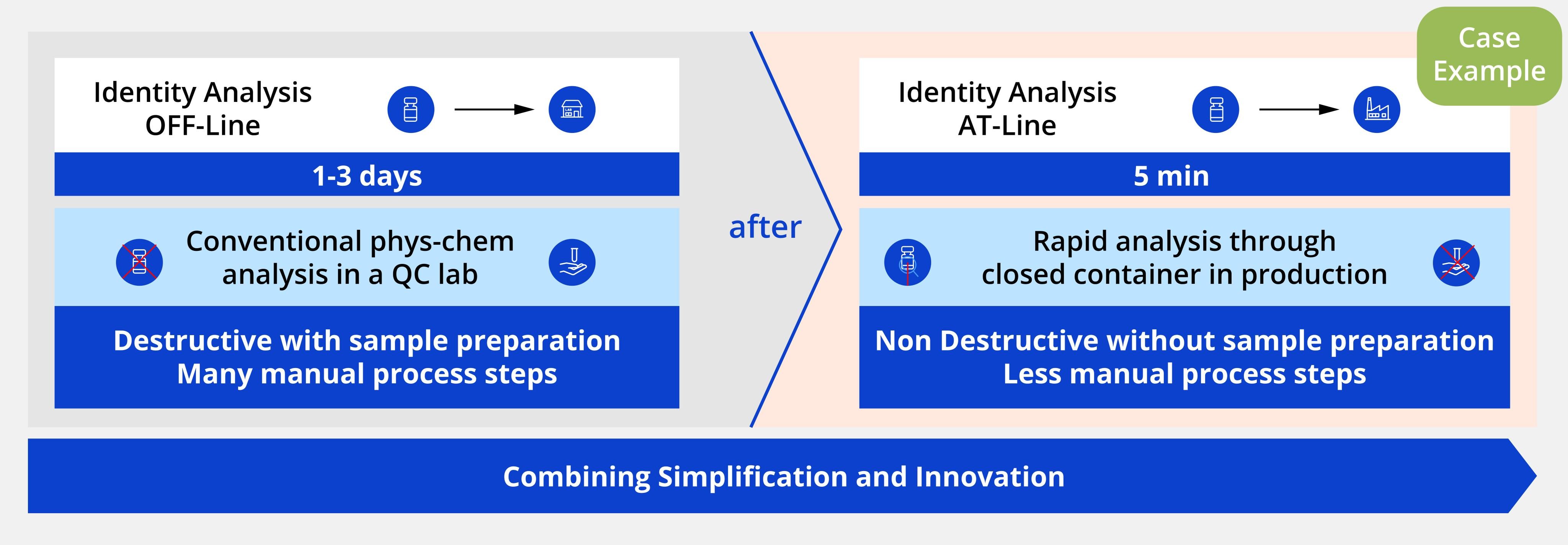
In a typical scenario, lab-based testing would require 1-3 days due to a series of complex sample preparation steps and complex analytics, whereas performing identity testing at line was completed within just five minutes.
Looking Forward
The successful integration of our VRU technology with Roche’s PAT - combined with the CTP - enabled us to implement non-destructive, real-time quality control testing in alignment with our outlined approach and validating the effectiveness of our proof of concept.
Moving forward, to further advance this solution, Stevanato Group will collaborate closely with our customers to seamlessly integrate robotics with instrumentation, with our future collaborations ensuring that our data collection processes are not only efficient and accurate, but also fully compliant with GMP. We aim to enhance the overall quality control framework, delivering robust, reliable, and regulatory-compliant solutions in the field of pharmaceutical manufacturing.
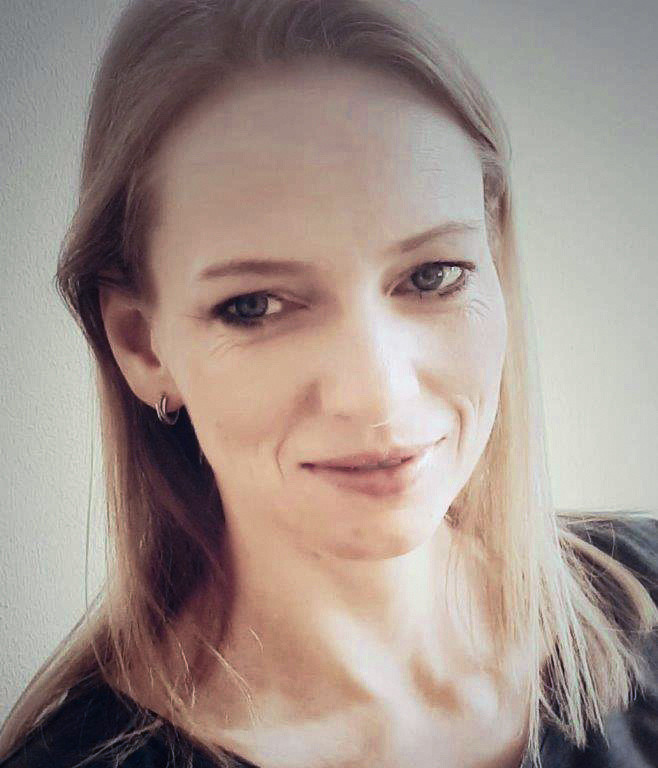
« I have the opportunity to work in an inspiring environment developing the idea of the “Vision Robot Unit Compendial Testing Platform” in collaboration with Stevanato Group. I sincerely appreciate our colleagues at Stevanato Group for their collaborative spirit, and the innovative and valuable input. A big thank you to both, Stevanato Group and Roche, for the invaluable contributions that transformed this idea into reality.
There is a pressing need for innovative non-destructive analytical technologies capable of efficient testing. Enter the “Vision Robot Unit Compendial Testing Platform”, a versatile solution facilitating real-time release testing. This platform embodies a flexible, fleet-oriented approach, aligning seamlessly with the vision of a futuristic factory. It caters to the manufacturing demands of both clinical trial and industrialization phases. Stevanato Group and Roche have joined forces to pioneer process innovation through platform concepts and robotic systems, revolutionizing the release of small batches. »
Susanne Gawenda, Roche