Executive Summary
Introduction: Ensuring the mechanical resistance of pharmaceutical glass vials is crucial for safe and efficient drug delivery. While allowing for high throughput and efficiency, the bulk Fill & Finish process exerts high level of stress on glass containers, such as glass-to-glass contact and vertical loads, which can lead to cosmetic defects and breakages. Superior vial quality mitigates the negative impact of this stress, improving filling process performance and output as well as reducing the risk of container breakage during transport.
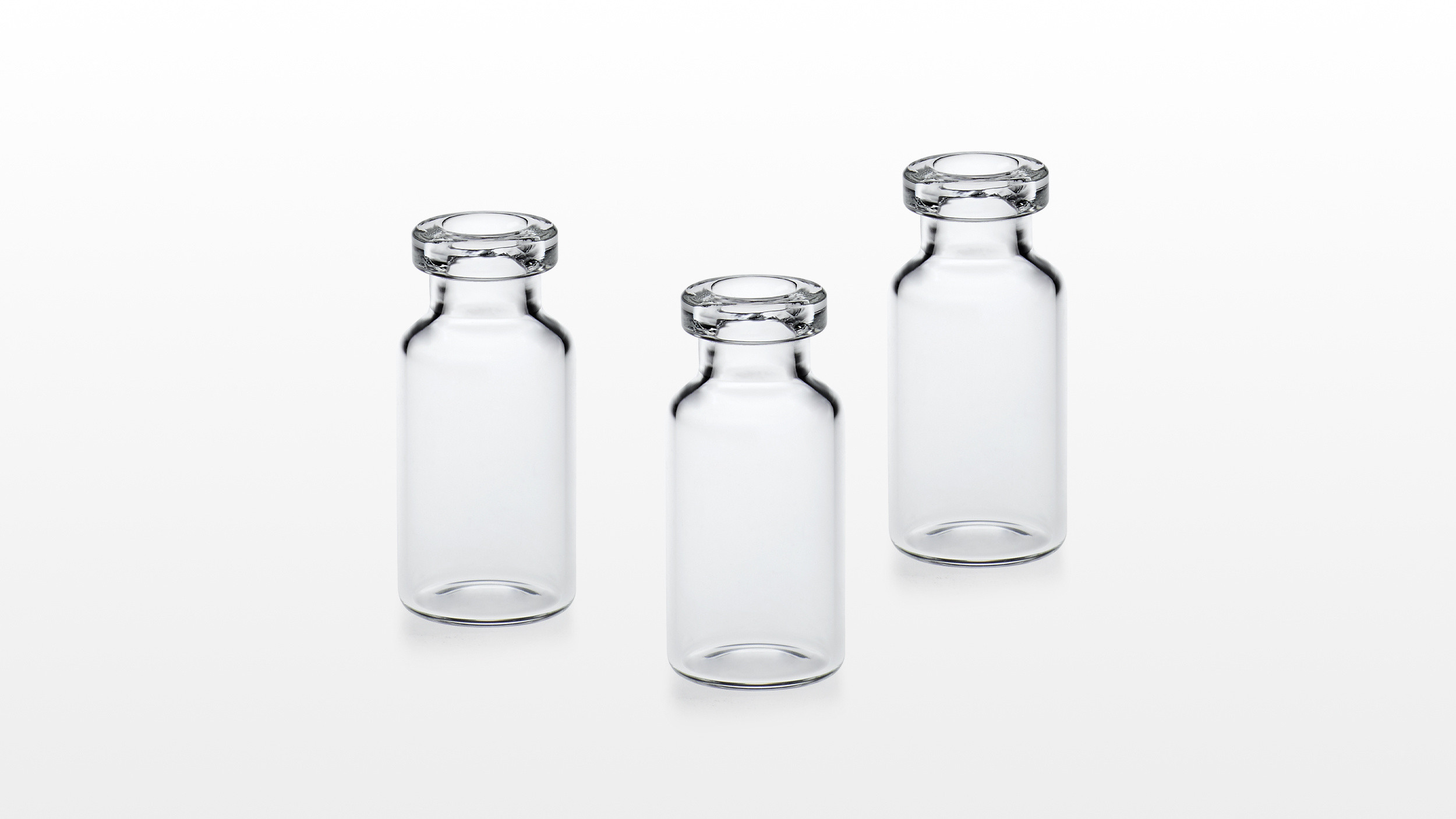
This study aims to experimentally demonstrate the improved mechanical resistance performance of Nexa®. By comparing the 2R ISO format vial in Nexa® and Fina® platforms, this study highlights how Nexa® vials provide superior mechanical resistance, which translates into several operational benefits.
Test Methodology
Mechanical resistance was assessed using two quantitative techniques
1. Vertical Compression Test (VC): This test measures the maximum force a vial can withstand before failure when subjected to axial stress.
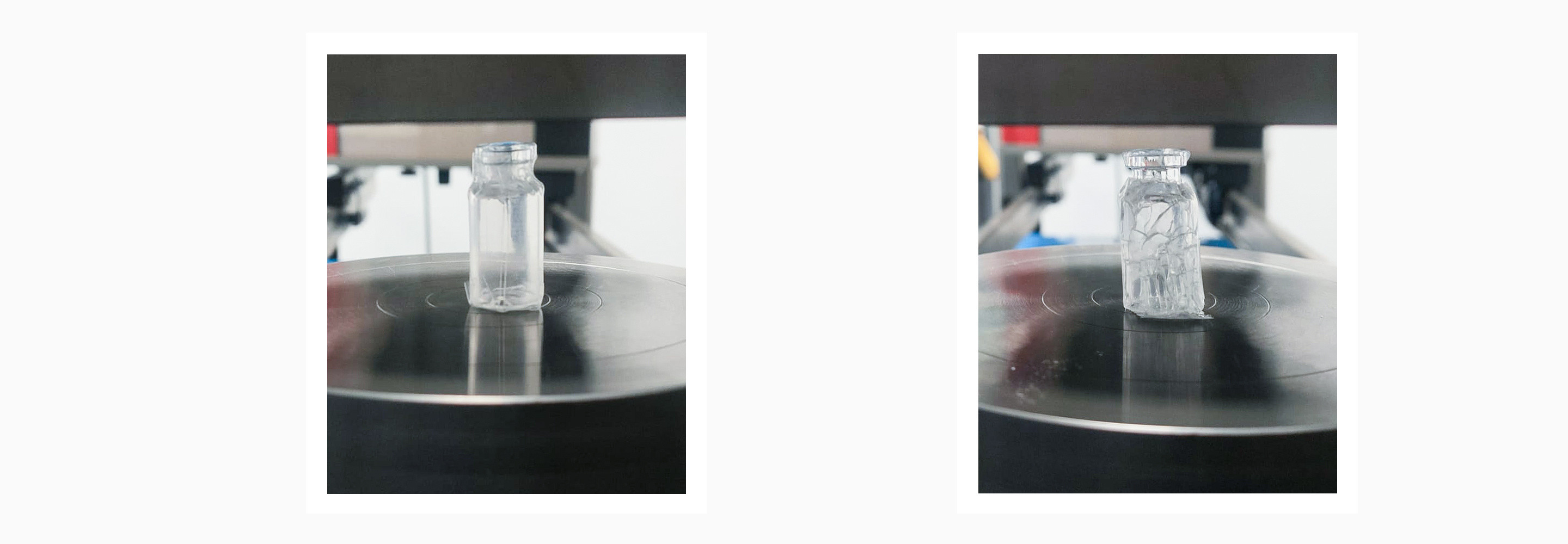
Figure 1: Sample before (left) and after (right) VC test.
2. Burst Test (BT): This test is performed to apply internal pressure to the glass container to obtain its maximum value of internal pressure resistance.
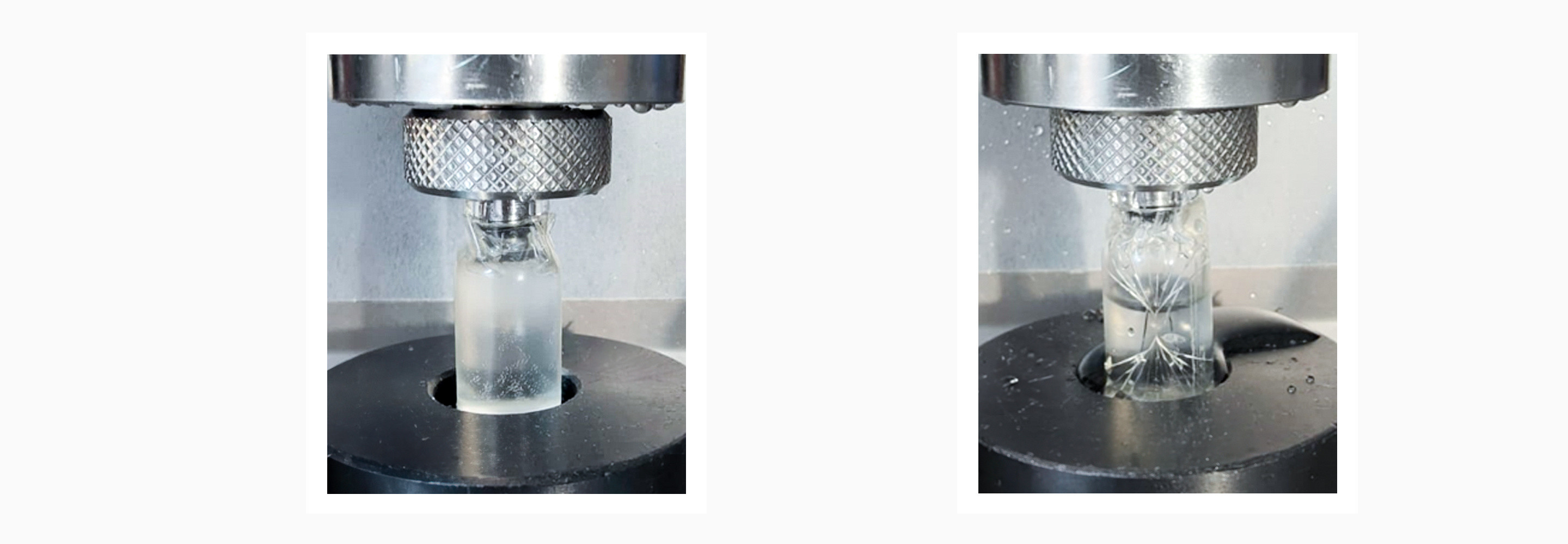
Figure 2: Sample before (left) and after (right) the burst test.
Both tests compared Nexa® and Fina® vials. From the results achieved (VC and BT), Nexa® vials showed consistent superior mechanical resistance.
Key Results
2R ISO vials
- In the Vertical Compression Test, Nexa® vials demonstrated an average maximum force of at least 3x Fina®.
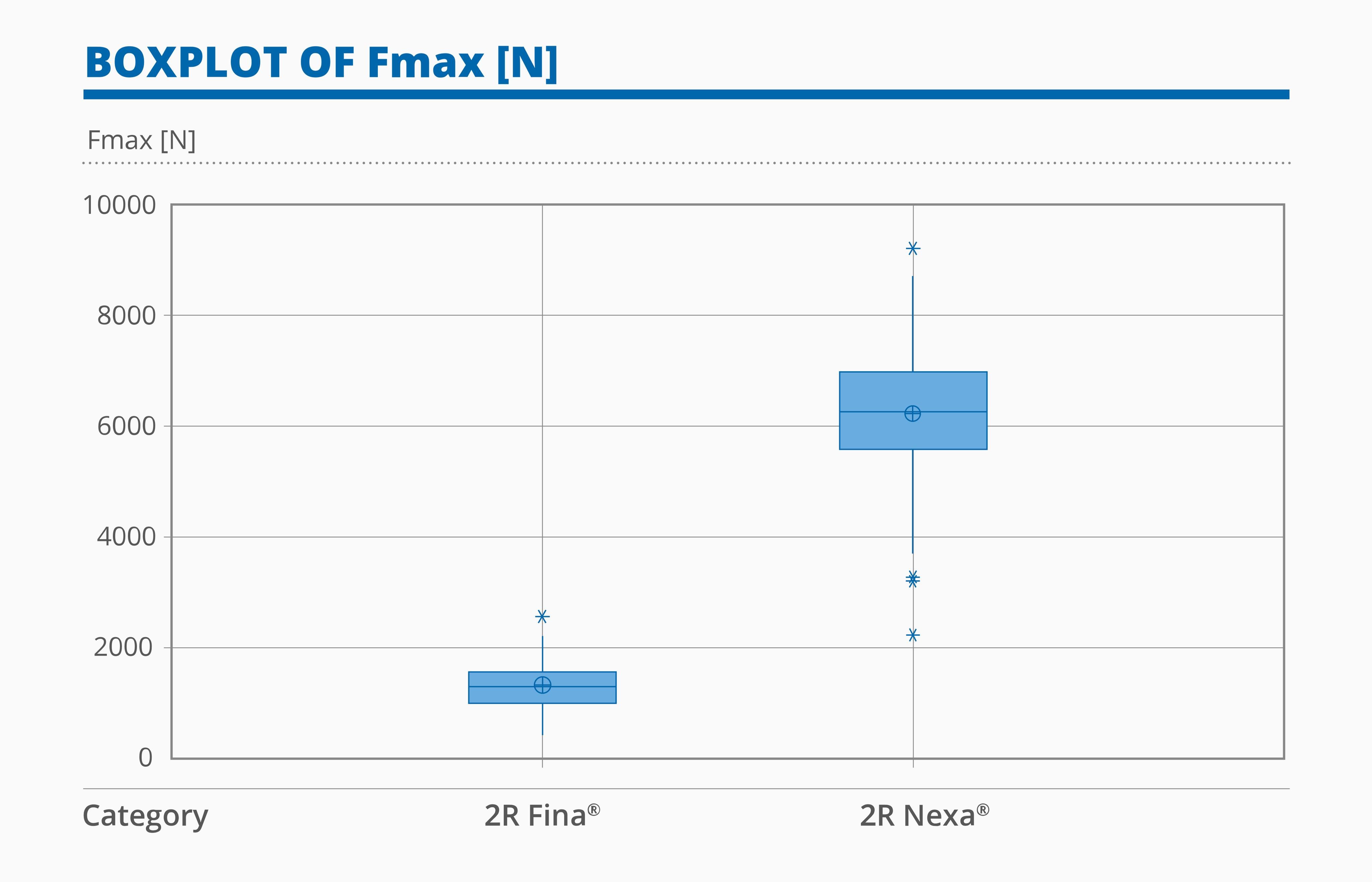
Figure 3: Boxplot of Vertical Compression results for 2R Fina® and Nexa® vials.
- In the Burst Test, Nexa® vials are characterized by a higher mean value, in terms of maximum pressure, than Fina® vials.
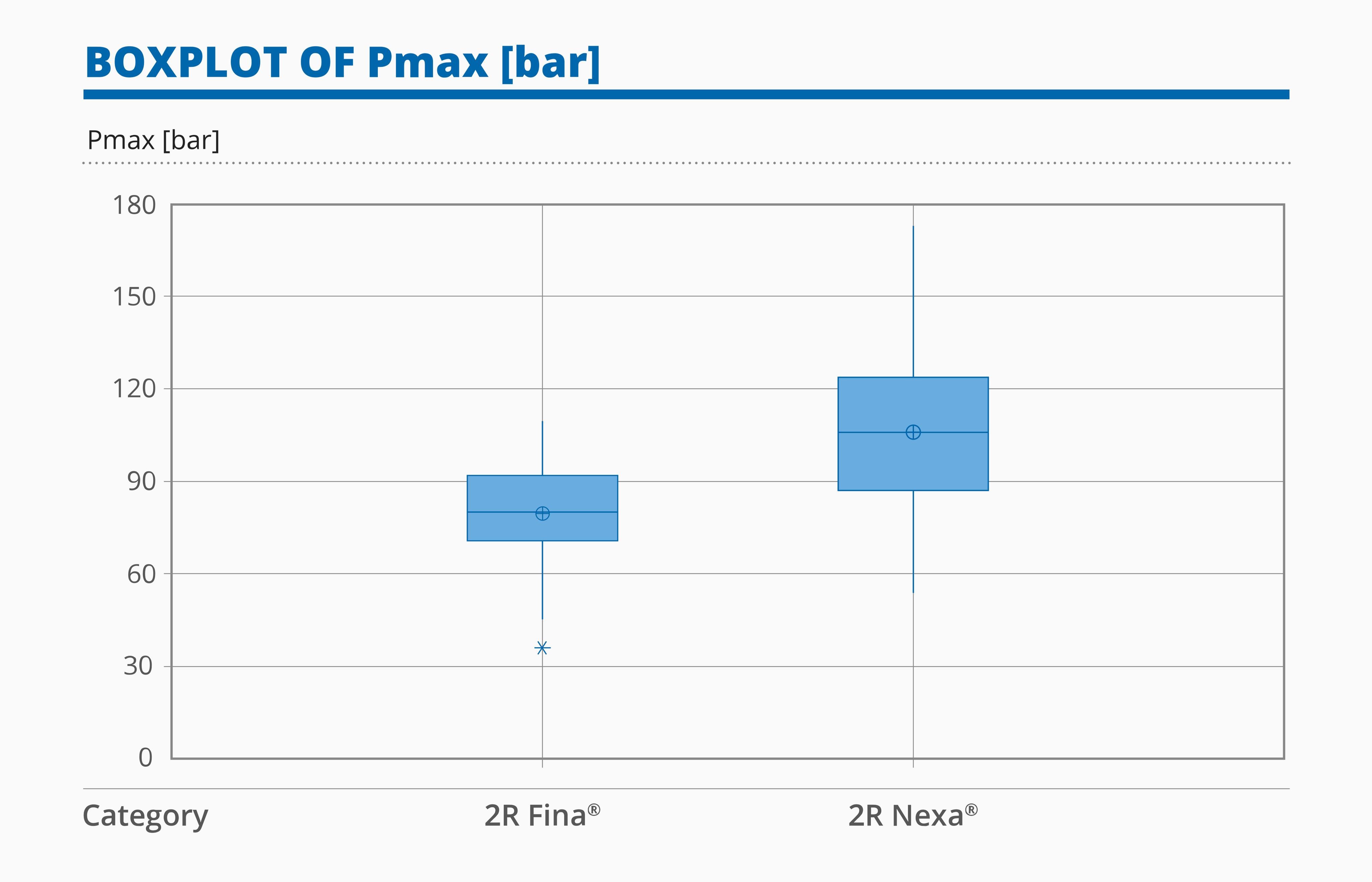
Figure 4: Boxplot of Burst Test Results for 2R Fina® and Nexa® vials
Operational Benefits of Nexa® Vials - Thanks to their improved cosmetic quality and mechanical resistance, Nexa® vials provide several advantages:
Reduced Total Cost of Ownership (TCO): Fewer cosmetic rejections and in-line breakages reduce waste of both container and final product, which in turn lowers costs and prevents lost revenues.
Improved Efficiency: Nexa® vials result in fewer lines-stops, downtimes, and labor required to fix the filling line after breakage occurrence.
Higher Safety: The superior mechanical strength of Nexa® vials reduces the risk of harmful products being dispersed due to container breakage.
Conclusions
This study analyzed the improved mechanical resistance of Nexa® vials by comparing them to Fina® vials through vertical compression (VC) and burst test (BT). According to the results achieved, Nexa® vials have superior mechanical resistance, even 3x Fina® with regards to Vertical compression (VC).
Thanks to its improved mechanical resistance, the Nexa® vial platform offers advantages in terms of:
Lower risk of breakage and cosmetic rejections reducing non-quality costs, and maximizing redictivity of high-value drug products
Lower risk of breakage to preserve people’s safety when dealing with cytotoxic products and to guarantee container integrity during challenging freezing processes.
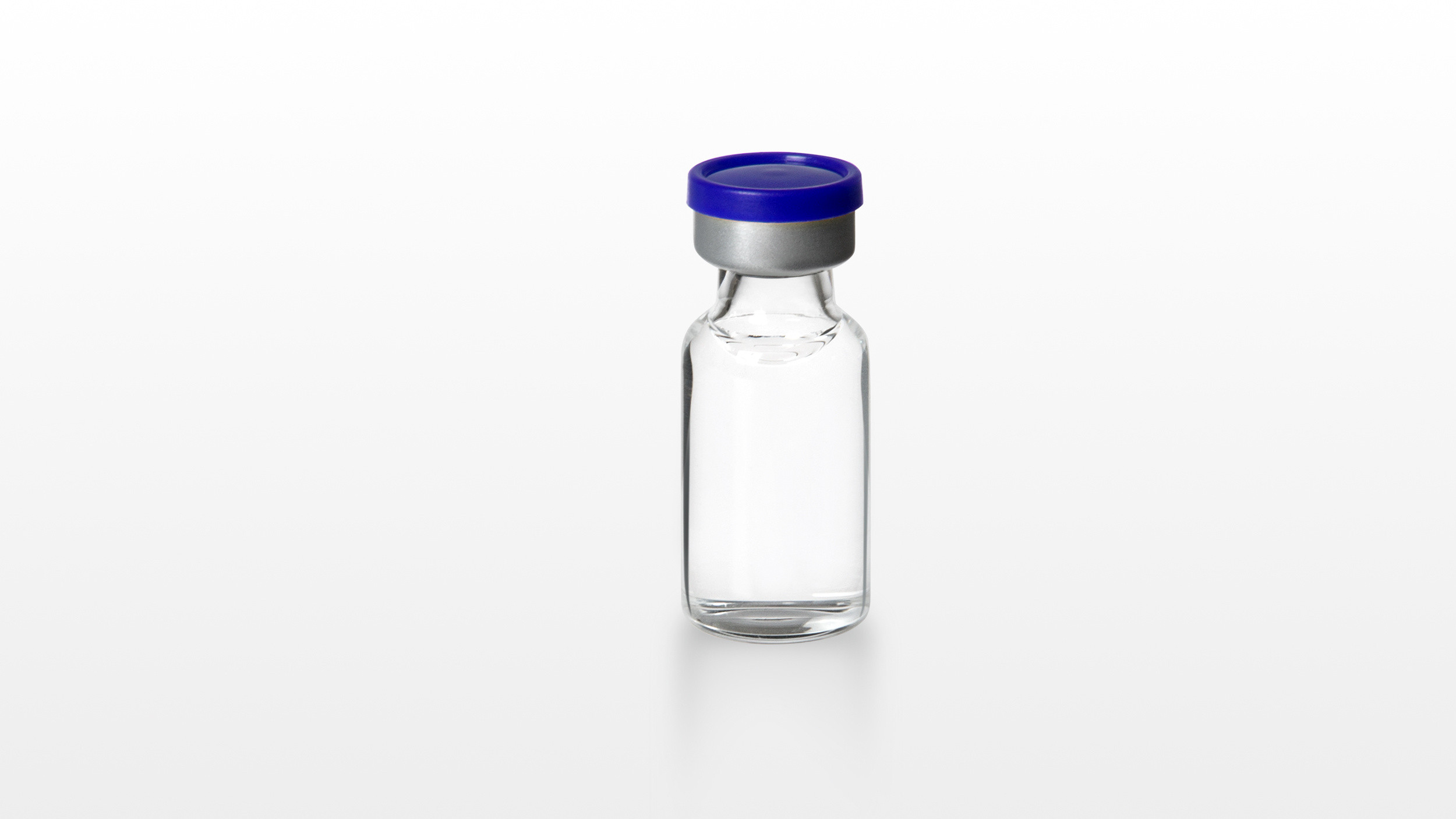
Nexa® vial platform is Stevanato Group next level of quality specifically designed for most of high value products such as biotech, high-value vaccines, cytotoxic and next generation drugs.
Thanks to their improved mechanical resistance and cosmetic quality Nexa® vials minimize product waste and product release into the environment during fill & finish process and final visual inspection.
Additionally, Nexa® vials ensure lower vial breakage risk at challenging temperatures during freezing and cryo treatments.