Time to market is critical in the fast-paced world of drug delivery devices – so streamlining the product development process by having design and development teams under one roof makes business sense.
That’s why here at Stevanato Group our design and development teams collaborate every day to optimize workflows. It means they are ready to go from day 0 – before a project even gets underway – saving our clients time and money, as well as ensuring the highest quality and reliability of the finished product.
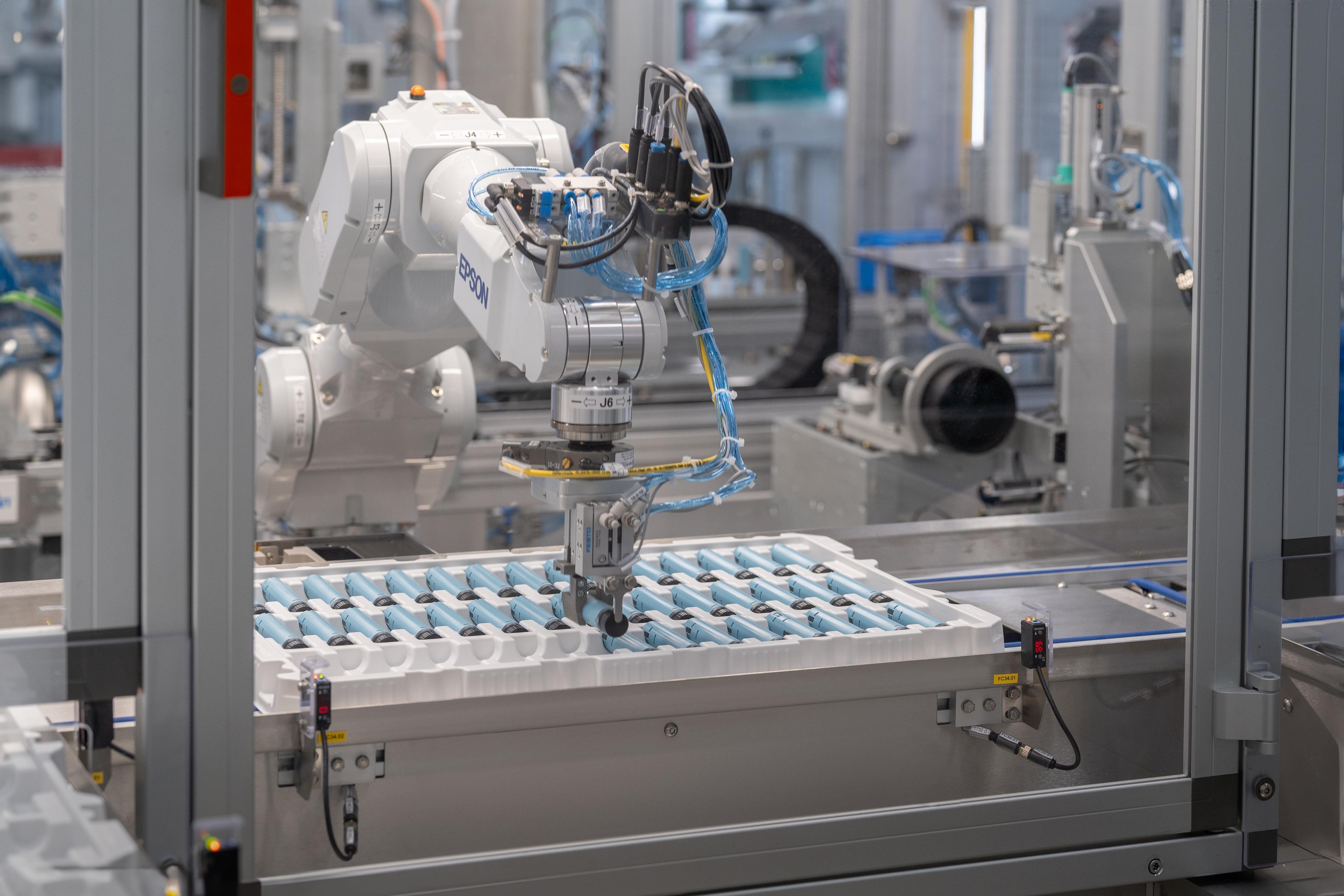
Considering manufacturing processes from the outset – and identifying potential challenges – reduces the expense and delays caused by design adjustments late in the product development cycle.
Proactive problem-solving reduces the risks associated with transitioning from prototype to full-scale production. And continuous feedback between design and industrialization teams fosters innovative solutions that are both feasible and practical.
An example of this integrated approach in action is the development of Stevanato Group’s Alina® variable dose pen injector suitable for diabetes and weight management therapies.
Our multidisciplinary team brainstormed various design concepts for the new feature. Each idea was evaluated not just for functionality but also for manufacturability – ensuring the concepts were realistic and achievable.
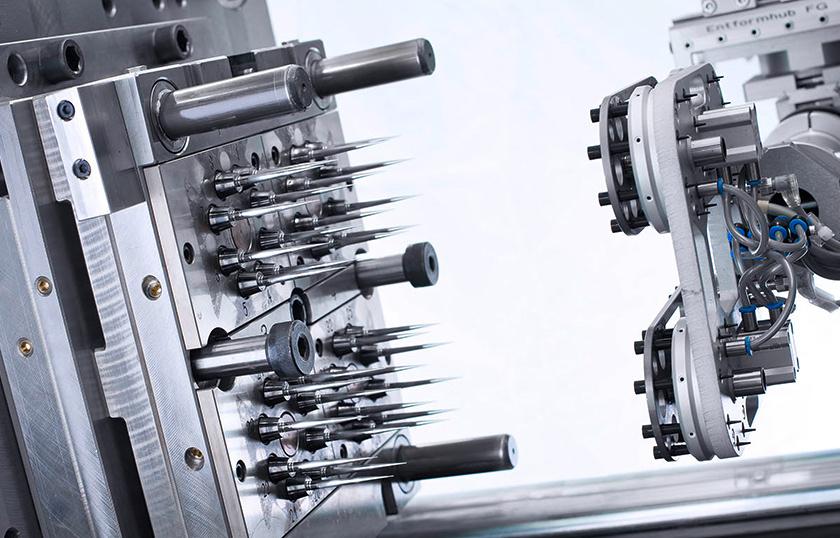
The intricacies of molding and assembly were considered as well as the potential challenges and benefits of each design – focusing on material choices, production efficiency, and assembly processes.
Next came the design for manufacturability analysis to optimize tool design and assembly cycle time and minimize the risk of functional issues.
To bridge the gap between design and final production, the Stevanato Group team created prototypes using technologies closely resembling the intended manufacturing processes. This step was crucial in identifying and addressing potential issues at an early stage.
The prototypes then underwent rigorous testing to assess performance and reliability. This included mechanical testing, patient trials, and stress tests to ensure Alina® met all required standards and patient expectations.
Using advanced simulation tools, the device’s behavior was modeled under various conditions, including dynamic drop scenarios. This provided invaluable data – enabling the device to be refined for optimal performance and durability.
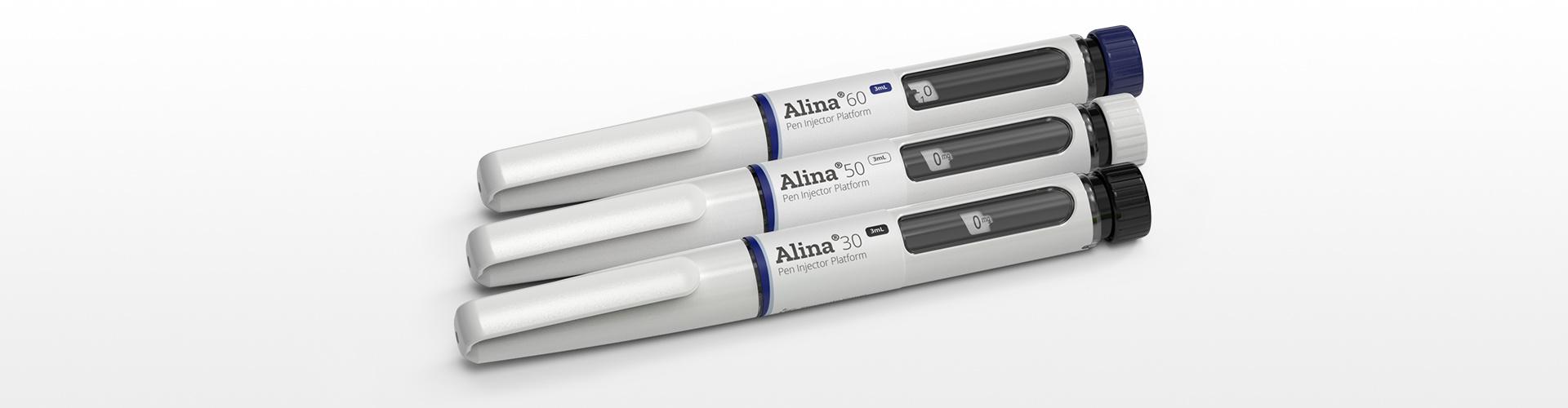
Based on the insights gained from testing and simulations, the necessary adjustments could then be made to the design. This iterative process ensured the final design was robust and manufacturable without compromising functionality.
To move from prototype to production, multi-cavity tools were developed for molding the components, coupled with a semi-automated assembly process. This setup not only enhanced production efficiency but also maintained high-quality standards.
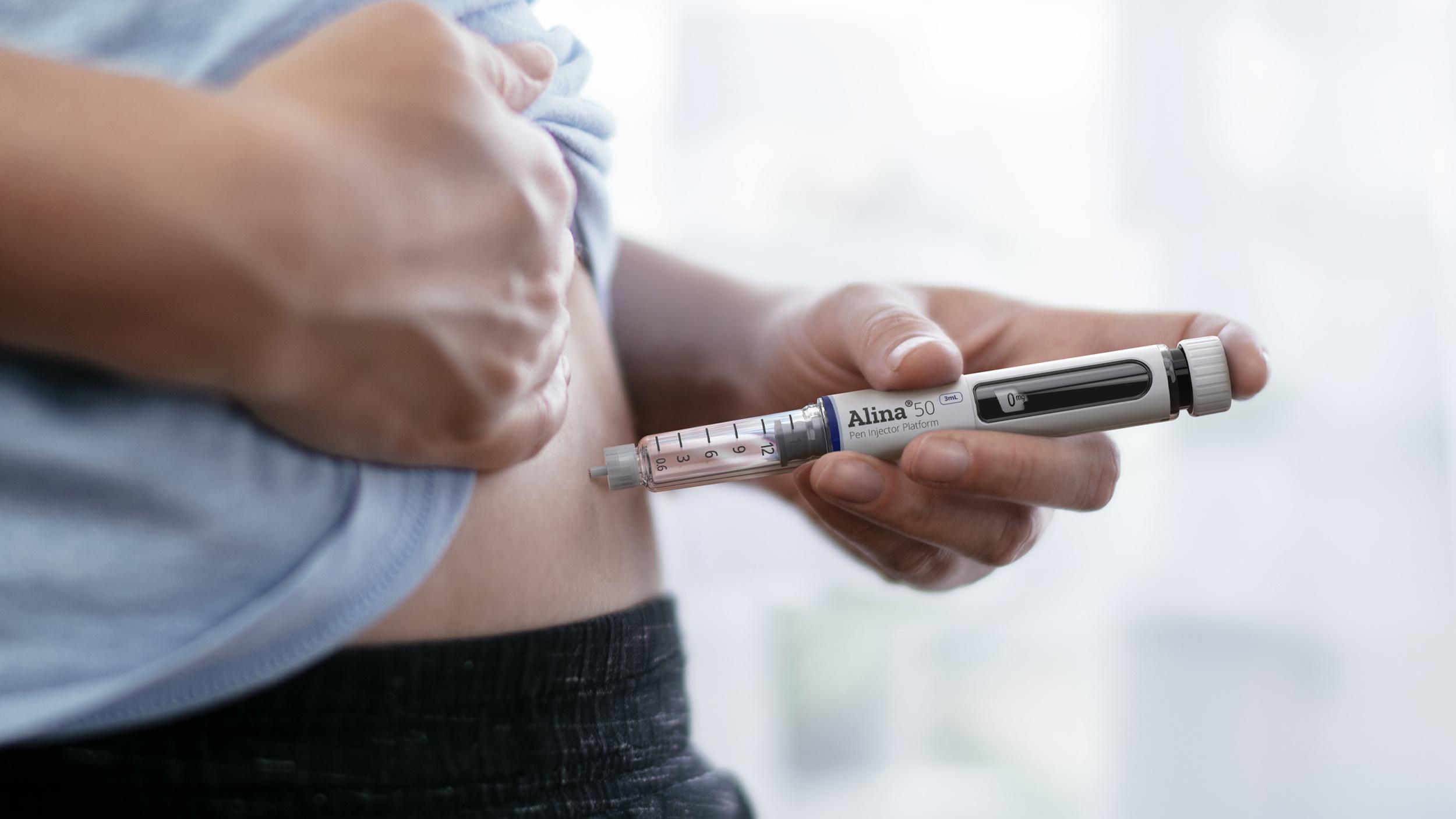
The Alina® pen injector example highlights the transformative effect of Stevanato Group’s integration of design and industrialization from day one of product development.
Close collaboration between our design and manufacturing teams delivers a high-quality, innovative product in a cost-effective and timely manner. This approach is not just a strategic advantage but a commitment to excellence in the ever-evolving field of drug delivery devices.
By continually refining our processes and embracing innovative solutions, Stevanato Group remains at the forefront of the industry – dedicated to providing reliable and advanced drug delivery systems that meet the needs of patients and healthcare providers worldwide.
Authors:
Tommaso Borghi, DDS Product Development Director - Stevanato Group
Marco Pirinoli, IVD & DDS Process Development Director - Stevanato Group